Companies move their data to the cloud. Most businesses today have at least some of their information hosted at Micrsoft’s Azure, Google Cloud or Amazon’s AWS. For large deployments, storage cost can be a significant saving. The ability to easily implement geo-redundancy and have scalability and simplified management are distinct advantages.
Back in 2004, when I first deployed an RFID solution, I asked the same question I hear from customers today: can I store additional data on the tag? Back then as well as today the answer is yes. However, the performance to write to our HF tags was poor; it was not technically feasible to do so. With HF we opted to use the Unique ID (UID), a pre-encoded identifier written to the tag by its manufacturer and did link it to the product data in our systems.
Today, most companies use the GS1 system and write the 96bit Electronic Product Code (EPC) to their RFID tag. This code is especially useful as the core of the EPC is an identifier already used in most enterprise systems. It uses the EAN or UPC plus an additional serial number. Without the need to sync information about individual tags, companies can use look-ups based on the EAN or UPC to find product information and product-related data and update for example their stock levels.
In Automotive applications, many companies have opted for an ISO/IEC data structure using 240bit of memory (see also VDA Recommendation 5500). Automotive companies tend to also use up to 512bit of user memory of the tag to store additional information required in the production lines. The better write performance of modern ICs made it possible to write more data in a reasonable amount of time.
Below are some of the many reasons, why you should opt to only use an identifier on the IC and link this to the Digital Twin.
Storage Cost
Storage in the non-volatile memory (NVM) of RFID ICs is incredibly expensive. Memory on the IC is estimated to be 100 times the cost of cloud storage with relatively poor i/o performance. On many current ICs, the NVM makes up approximately half the size of the die and the size of the die is one of the driving cost factors.
Data Access
Data stored on the IC is only accessible while the passive tag is in the field of view of an RFID reader and antenna. Visionary companies introduce RFID to gain visibility and data for analytics and predictions. Data stored in ICs that are offline, will not be available for analytics or algorithms for machine learning
Scalability of Memory
Memory on the IC doesn’t scale. Transitioning between IC generations has been a struggle for many companies. They need to update their deployments and re-tune read points as new generations of ICs perform better. Most RFID IC vendors chose to reduce the memory available on ICs to achieve cost targets and enable customers to scale. Companies can associate unlimited data points to an identifier stored in the cloud to record information about an item, such as the identity, ownership and history to generate data for analytics as well as additional services and experiences.
Read and Write performance
The performance of cloud storage is significantly better than what you find in RFID ICs. You won’t be able to perform the same, scalable number of read and write operations on the NVM of an RFID IC as you are available in modern storage systems or the cloud.
As adoption scales and vendors have to print and encode billions of tags a month, the time it takes to write data reliably to the IC will become a challenge. Companies have developed complex and expensive encoding equipment that meets the needs of current adoption but won’t be able to scale to the volumes and speeds required for FMCG production lines.
So, back to the UID?
RAIN RFID ICs compliant with the GS1 EPC Gen2v2, also ISO/IEC 18000-63 have a Tag ID (TID) pre-encoded at the point of manufacture. This ID already provides a unique identifier for each tag IC manufactured. Further reducing the memory of RFID tags will allow companies to reduce the cost. This change will require customers to adapt and be able to support two operating models:
- EPC Model: Look up an identifier written to the tag with a number series usually managed by the manufacturer of a product. Look-ups can be linked to an existing database of EAN and UPC data
- TID Model: connect an externally managed number to the associated digital twin that provides all business-relevant information. TID look-ups require companies to either sync tag specific data to all sites and devices or ensure cloud connectivity.
Always-on connectivity of devices and locations is a vital need to operate the TID model. Many business processes require this connectivity already today which means to abandon the EPC as an identifier on the RFID tag will become a viable option in the mid-term.
Impact on solution architecture
Consider both operating models when architecting an RFID implementation and ensure you can support both operating models and mixed tag populations in your deployment. In an early stage of a project this won’t have a significant impact on cost but will ready you to leverage new and low-cost IC options in future.
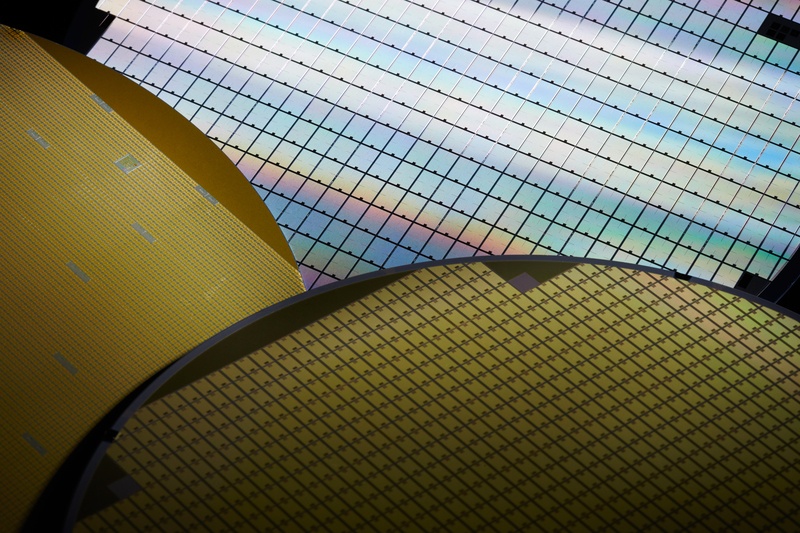